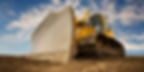
If your company operates heavy equipment, you know all about the challenges that can reduce your profit margin. Missing scheduled maintenance can turn small problems into major breakdowns; inaccurate billing can lead to overspending or under charging and unnecessary idling can elevate fuel costs.
Using the right equipment tracking and monitoring solution can help prevent costly issues and dramatically increase profit. Whether it’s a forklift, light tower, bulldozer, or generator, you need to know what your machines are doing, where they are, and how efficiently they are running.
Track Actual Equipment Usage:
When equipment is left at a job site for days or weeks at a time, it is difficult to track how long the equipment was in use. Continuous equipment monitoring provides insight into prolonged idle times, allowing you to cut fuel costs and ensure critical maintenance is never missed. With visibility into engine diagnostics data such fluid levels, temperatures and error codes, you can streamline operations and fully utilize all equipment. All of this real-time data into usage can help you extend the life of your equipment and reduce operational costs.
Recover Lost or Stolen Equipment:
Has a piece of your equipment ever been out of service because it was stolen or misplaced? Manually tracking down equipment leads to unnecessary downtime and takes away man hours that could be spent on the job.

Equipment tracking not only provides real-time GPS data while the equipment is operating, but also while vehicles are not in use, giving a precise location at all times. To prevent unauthorized use and theft, you can configure alarms that trigger instant notifications if equipment leaves a job site.
Accurately Bill Customers:
Billing customers on flat rates can lead to under or over charging. This can either take money out of your pocket or make customers upset for overpaying. Equipment tracking systems that integrate with engine run-time hours produce to-the-minute readings, allowing companies to accurately bill for equipment use. Equipment monitoring solutions mean that the days of billing on flat rates are gone. With accurate usage data you can start putting more money in your pocket.
Scheduling Preventative Maintenance:
Without insight in run-time or engine hours, you would never know how long equipment was actually running. You’re forced to make your best guess on when maintenance is needed. Move from corrective maintenance to preventative maintenance with a system, like Maintenance Manager, which provides diagnostic information and can notify users when maintenance is due. This can ensure small problems don’t become expensive equipment failures and your equipment keeps up and running smoothly.
You’re working to increase profits and run the most efficient and productive operations. Equipment management systems, like OneView, grant the insights and data needed for your company to maximize operations and climb to the top.
To see how your business could benefit from an equipment monitoring solution, schedule a live web demo today!